Unser Haupt-Problem mit dem Drucker war von Anfang an die immer wieder durchgescheuerte PLA-Faser. Dadurch mussten wir ca. jeden zweiten Druck abbrechen. Wir haben mittlerweile diverse Dinge verbessert, wodurch es besser geworden, aber nie ganz verschwunden ist:
- Die Faden muss exakt zentriert in die Metallöffnung geführt werden
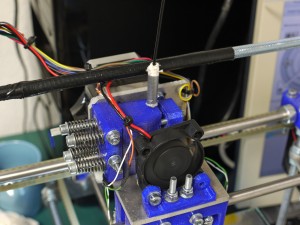
PLA-Faser-Antistaubwurst
- Der Anpressdruck des Drive Gear an die Faser muss stimmen
- Der Extruder darf nicht zu kalt sein (210°C für PLA ist gut)
- Staub der über die PLA-Faser in den Extruder gelangt, verstopft diesen in regelmäßigen Abständen. Der wird effektiv von einem eng gewickelten, getapedten Klopapierwürstchen um die Faser direkt über dem Extruder aufgehalten.
- In der Druckerfirmware Marlin kann eingestelt werden, dass unter eine berstimmten Extrudertemperatur nicht extrudiert werden kann. Das ist höchst sinnvoll, da die Faser bei zu kaltem Extruder sofort durch ist.
Bei Thingiverse haben wir das V9 Extruder Upgrade for MK7 Drive Gear gefunden und sofort das Drive Gear (links im Bild) bestellt. Um den Rest des Extruder-Upgrades drucken zu können, wurde zuerst provisorisch das neue Drive Gear in den alten Extruder eingebaut. Dabei stellte sich heraus, dass das alte Gear (rechts im Bild) an der PLA-Kontaktstelle schon deutlich abgenutzt war.
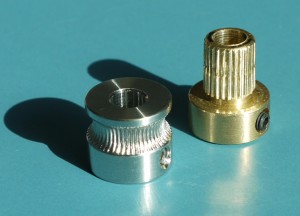
links: Makerbot MK7 Drive Gear, rechts: Mendel V9 org
Nachdem der Steps-per-mm Wert angepasst wurde, konnten die übrigen Extruderteile durchscheuerfrei gedruckt werden.
Vor kurzem sind wir von Skeinforge auf Slic3r zum umwandeln der .stl Dateien umgestiegen. Das Programm ist sehr sehr sehr viel einfacher zu bedienen und lieferte am ersten Abend schon bedeutend bessere Druckergebnisse als Skeinforge nach vielen Monaten der Optimierung. Man hat zwar lange nicht so viele Möglichkeiten, Skinning vermissen wir beispielsweise, aber die vorhanden Einstellungen greifen sauber und druchdacht ineinander.
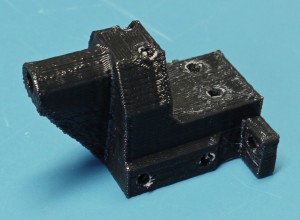
Teil des Extruder-Upgrades mit Slic3r umgewandelt
Das gezeigte Teil wurde gerade eingebaut und der erste Druck (eine Centerplate für den Warpzone Quadkopter) scheint gut zu laufen. Als letztes wurde das Printbed durch eine Glasplatte upgegraded. Die Druckteile haften nun genau richtig fest: man braucht nun keine Angst mehr zu haben den Drucker beim ablösen auseinanderzureißen, gleichzeitig hat sich noch nichts während des Drucks von selbst abgelöst. Auch sind die Druckteile nun sehr glatt auf der Unterseite und Verschmutzungen des Printbeds sind wesentlich unkritischer. Es handelt sich um eine stinknormale 4 mm dicke Glasplatte, ein Dachbodenfund:
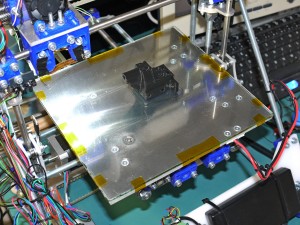
Printbed mit Glasplatte